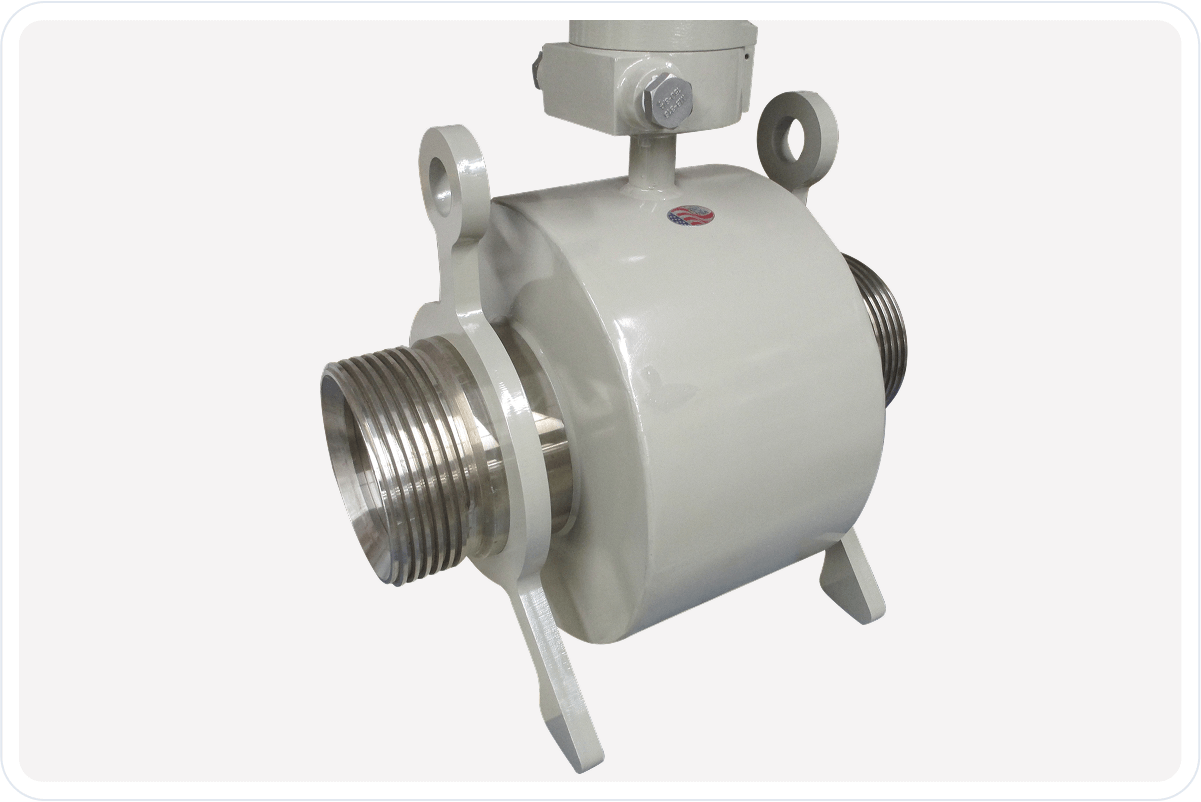
TECO HP Severe Application Meter (SAMHP)
The world’s highest pressure magnetic flow meters with superior erosion and abrasion resistance for corrosive applications and slurries featuring custom ceramic liner, metallurgy and electrodes, handling pressures up to 15,000psig.
Product Summary
Download Product Summary SheetA magnetic flow meter with abrasion resistant ceramic trim that exceeds the capabilities of Alumina or Yttria Zirconia. Capable of withstanding a variety of corrosive slurries, acids, bases and solvents.
Applications
Fracking Application
The SAM is TECO’s patent pending magnetic flow meter with abrasion resistant ceramic trim that exceeds the capabilities of Alumina or Yttria Zirconia. Capable of withstanding a variety of corrosive slurries, acids, bases and solvents, the SAM is the world’s first magmeter specifically designed for Severe Fracking Applications.
Measurement of extremely abrasive slurries in Mining, Dredging, Fracking, and Oil and Gas Exploration (will not measure oil or gas).
Specifications
Download Spec SheetSize Range | 2” – 4” with FIG. 1502 Female Connections. |
---|---|
Accuracy with DC signal converter | 1/2% of rate (1 – 15 M/sec scale) |
Accuracy with AC signal converter | 1% of rate (1 – 10 M/sec scale) |
Pressure Rating | 15,000 psi Cold Working Pressure at temperatures up to 100° F |
Max Process Rating | 400°F at a Reduced Working Pressure per FIG 1502 specification. |
Max Process Temp Gradient | (estimate 100° per min.) |
Wetted Materials | Electrodes: Billet Tungsten Carbide Electrodes; Lining: Magnesia partially stabilized Zirconia (MgPSZ) |
Environmental Limits: Temperature | -40°F to 140°F |
Environmental Limits: Submergence | IP68 / NEMA 6P |
Weight | 236 lbs |
Process Pressure | Full Vacuum to 15 ksi ( 0 Bar to 1034 Bar ); Tested to 1.5 x MAOP = 22.5 ksi |
Vibration | 1.5g at 10 Hz to 150 Hz |
Environmental Limits: Hazardous Environments | See model code selections |